Alloy 625 ESU | 2.4856 (NiCr22Mo9Nb) from stock
Applications:
The corrosion-resistant high-performance material Alloy 625 has improved material properties due to the electroslag remelting process (ESR).
The ESR version is used when a better material purity, particularly high tensile strength and toughness are required.
The Alloy 625 ESU has very good corrosion resistance and good resistance to attack phosphorus, sulfur and hydrochloric acid. The material can be welded, taking into account a suitable weld preparation. A heat treatment before and after the welding process is not required.
Areas of application
2.4856 ESR (Alloy 625) is mainly used in areas in which exceptional resistance to all corrosion phenomena, in combination with excellent creep strength and extreme temperature loads, is required. The nickel-based alloy 625 is also used in the food and nuclear industries.
At lower temperature loads, the alloy Alloy 825 with lower alloying elements of nickel and molybdenum and the correspondingly lower strength properties can be used.
Weldability | good |
Machinability | 5 (1 = bad - 10 = good) |
Polishability | yes |
Corrosion resistance | very good |
Corrosion class | 10 (1 = bad - 10 = good) |
Mechanical properties at room temperature (solution annealed / quenched):
Rp0,2 | A | Hardness | KV |
N/mm2 | % | HRC | J |
≥ 345 | ≥ 25 | max. 35 | ≥ 100 |
Physical Properties:
Density (kg/dm3 ) | 8,4 |
Thermal conductivity at 100°C (W/m K) | 12,4 |
Thermal conductivity at 800°C (W/m K) | 26,8 |
Specific heat capacity at 100°C (J/kg K) | 496 |
Specific heat capacity at 800°C (J/kg K) | 663 |
Specific heat capacity at 1200°C (J/kg K) | 705 |
Elasticity module at 20°C (MPa) | 209000 |
Elasticity module at 800°C (MPa) | 153000 |
Special features:
Resistance to mineral acids
Resistance to changing temperatures within extreme limits
Good mechanical and technological properties
Processing:
Cold forming is possible | is possible |
Cold heading is possible | is possible |
Machining possible | with a technologically designed procedure |
Open-die and closed-die forging | is possible |
Machine processing | no |
Heat treatment
Temperature in °C | Cooling | |
Hot forming | 1150 - 950 | air, water |
Heat treatment | ||
Solution heat treatment (+ AT) | 1080 - 1160 | air, water |
Welding: The Alloy 625 is easy to weld. The material 2.4831 is recommended as filler metal, taking into account the corresponding weld seam preparation for nickel alloys.
Forging: Before forging, the steel should be heated to a minimum of 950° C to 1150° C. This should be held for 60 minutes per 100 mm of decisive wall thickness. The forging process takes place at 1180° C to 950° C with subsequent rapid air or water cooling.
Cold forming: Due to the high tendency to work hardening (see also machining), special design of the heat conduction and higher forming forces are required.
Corrosion resistance: The corrosion resistance is far superior to conventional chromium-nickel-molybdenum steels (1.4571; 1.4539; 1.4404 etc.) and the resistance to intergranular corrosion, erosion, crevice and stress cracking corrosion is extremely high.
Machining: Machining (preferably in the annealed condition) is difficult due to the high alloy content. Due to the tendency of the material to work hardening, it should be machined with lower feed rates and cutting speeds compared to the corrosion-resistant austenitic steel types.
Alloy 625 ESU 2.4856 | C | Si | Mn | P | S | Cr | Mo | Ni |
---|---|---|---|---|---|---|---|---|
min. | 0,03 | 20,00 | 8,00 | 58,0 | ||||
max. | 0,10 | 0,50 | 0,50 | 0,020 | 0,015 | 23,00 | 12,00 |
Alloy 625 ESU 2.4856 | Fe | Al | Co | Nb | Ti |
---|---|---|---|---|---|
min. | 3,15 | ||||
max. | 5,00 | 0,40 | 1,00 | 4,15 | 0,40 |
Alloy 625 ESU, Flat, forged
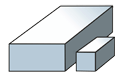
The processing with the saw is a mechanical processing of the material, which results in a significantly lower unintended deformation and increased hardness for the existing structure, such as the thermal cutting.
Thus, the machined workpiece has a homogeneous structure even at the edge, which does not change in the continuation of the material.
This circumstance allows immediate finishing of the workpiece with milling or drilling . So it is not necessary to anneal the material or make a similar operation beforehand.
Do you have any questions?
We are happy to answer your questions and make you an offer for these and other materials. Contact us now for more information.

Your contact person Heidi Sommer+49 (0) 35263-665-33sommer@stahlportal.com
Notice: Specifications contained in following data sheet are provided as a description, liability is excluded!